اتصل
هاتف
+0086-371-86162511
عنوان
تشنغتشو ، الصين
process calculations of cement grinding

Cement grinding optimisation ScienceDirect
To optimise cement grinding, standard Bond grinding calculations can be used as well as modelling and simulation techniques based on population Crushing and Grinding Calculations—April 1962. Additions and Clinker grinding constitutes approximately 40 percent (PDF) Cement grinding optimisation ResearchGate
احصل على السعر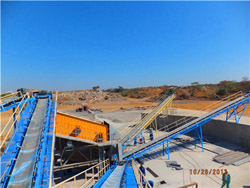
Analysis of material flow and consumption in cement
Low (2005) performed the first comprehensive material flow analysis for concrete, and calculated the amounts of raw material, water, and energy required as This study aimed at improving both the energy efficiency and product quality of the end product for a given cement grinding circuit by applying an accurate sampling Energy and cement quality optimization of a cement
احصل على السعر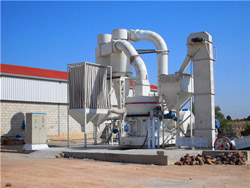
Grinding process optimization IEEE Xplore
Grinding process optimization — Featuring case studies and operating results of the modular vertical roller mill. Abstract: As a world-wide leader in grinding In this chapter an introduction of widely applied energy-efficient grinding technologies in cement grinding and description of the operating principles of the related equipments and comparisons over Energy-Efficient Technologies in Cement Grinding
احصل على السعر
Energy and cement quality optimization of a cement grinding
The pyroprocessing process in kilns and the grinding technologies therefore have to be optimized for best processing. This paper discusses the cement This study aimed at optimizing both the energy efficiency and the quality of the end product by modifying the existing flowsheet of the cement grinding circuit. As a Energy and cement quality optimization of a cement
احصل على السعر
Grinding process within vertical roller mills: experiment
Based on screening analysis, laser size analysis, grindability and rigidity tests of samples collected on line from a cement and a power plant, a simulation of the Abstract. Based on screening analysis, laser size analysis, grindability and rigidity tests of samples collected on line from a cement and a power plant, a simulation of the grinding process in vertical roller mills was carried out. The simulation calculation used a breakage function, B. The results indicate that the breakage function, B, andGrinding process within vertical roller mills: experiment and
احصل على السعر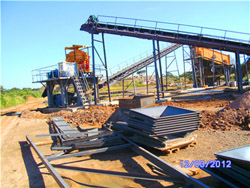
Breakthrough in Clinker Grinding Massachusetts Institute of
BREAKTHROUGH IN CLINKER GRINDING By: Richard P. Bohan, Director of Manufacturing Technology, Portland Cement Association, rbohan@cement, and John P. Kline, Principal, John Kline Consulting, johnpkline@gmail ABSTRACT Particle size reduction is one of the most energy intensive and inefficient processes in Pyro Calculations. Most Frequently Used Pyro Calculators Now Available Online For Evaluation and Process Control in Cement Industry. Size Calculations. Degree of filling DF%. Burning zone/Thermal loading TL. Volumetric loading VL. Material residence time in kiln RTK. Go To Online Calculators. Cooler Loading CL.cement plant calculations kiln, mills, quality, combustion, etc. all
احصل على السعر
(PDF) Analysis of the efficiency of the grinding process in closed
For open circuit grinding [34,35], there is no disagreement with the calculation of the circulating load and classification efficiency, both of which 2 can be characterized relatively accurately.As a general rule, there should be less than 25% of clinker that is below 1mm in size. Coarse clinker is more of an issue for ball mills. Some cement groups use a formula, such as Bond’s, to calculate the maximum ball size required in a ball mill, based on the average size of the clinker feed. However, one drawback with this approach is thatClinker size and cement grinding GCP Applied Technologies
احصل على السعر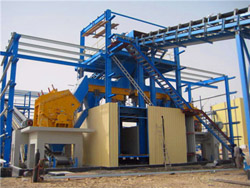
Indicate Contributions from Several Radial VHYHQ4&WRROV
increasing output, lowering breakdowns and optimizing the grinding process which eats almost 60% of power cost. (VRM) has proved to be a popular choice for finished cement grinding due to low power consumption but it is also very sensitive to vibrations and can deteriorate productivity if process optimization is varied slightly.Introduction. Cement world production currently increases up to approximately 4 billion tons/year. The electrical energy consumed in cement production is 110 KW/tone and about 30% of which is used for raw material preparation and about of 40% for final cement clinker grinding [1], [2], [3].This leads to important cost increase of the Preparation of polymer-based cement grinding aid and their performance
احصل على السعر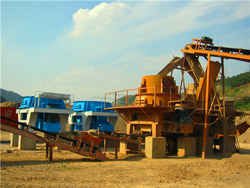
Determination of correlation between specific energy consumption
There are many studies about grinding process in cement industry. S öğü t et al. [11] calcu lated first-law (energy) and seco nd-law (exergy) efficiencies of a raw m ill by varying dead stateCement Grinding Section. File Name : 1_9_cementgrinding_4. Topic: Calculation of Cement Mill Output as a function of Grinding Media Load. Production of the ball mill Clinker grinding based on Grinding media loading. The theoretical production based on the grindability of the clinker is as given below.All Cement Formulae PDF PDF Mill (Grinding) Cement Scribd
احصل على السعر
The Effect of Various Grinding Aids on the Properties of Cement
Grinding aids, first introduced into cement manufacturing in 1930 [], are surface-active substances that facilitate particle comminution during the milling process.In the production of Portland cement, grinding aids are added in small amounts in the range of 0.01 to 0.10% by weight of cement, according to the PN-EN 197-1 standard [].This module introduces the typical raw materials for the cement process and the basic calculations necessary to proportion raw materials to achieve the clinker’s required chemistry. Cement Grinding Systems and Dispatch. Cement clinker is grinding in roller mills and ball mills, such as granulated blast furnace slag,AN INTRODUCTION TO THE CEMENT MANUFACTURING
احصل على السعر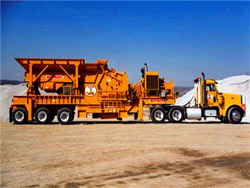
(PDF) Cement grinding optimisation Alex Jankovic Academia.edu
CEMENT GRINDING OPTIMISATION Dr Alex Jankovic, TON Minerals Process Technology Asia-Pacific, Brisbane,Australia e-mail: alex.jankovic@TON Dr Walter Valery, TON Minerals Process Technology Asia-Pacific, Brisbane, Australia Eugene Davis, TON Minerals Asia-Pacific, Perth, Australia ABSTRACT The current world consumption The pyro-process uses a wet or dry process to produce Portland cement. The dry process includes grinding and heating the raw materials first before feeding them into the (LCA) of traditional and ‘green’concretes: literature review and theoretical calculations. Cement Concr. Compos., 34 (4) (2012), pp. 431-442. View A review of the effectiveness of Life Cycle Assessment for gauging
احصل على السعر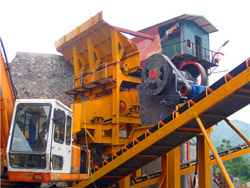
Cement Extraction, Processing, Manufacturing Britannica
There are four stages in the manufacture of portland cement: (1) crushing and grinding the raw materials, (2) blending the materials in the correct proportions, (3) burning the prepared mix in a kiln, and (4) grinding the burned product, known as “ clinker ,” together with some 5 percent of gypsum (to control the time of set of the cement).Cement manufacturing consists of raw meal grinding, blending, pre-calcining, clinker burning and cement grinding. In short, limestone and other materials containing calcium, silicon, aluminium andMODELLING A CEMENT MANUFACTURING PROCESS TO STUDY
احصل على السعر
Intensifying the cement grinding process
input for grinding. Data on cement clinker grinding kinetics when surface-active agents are used, as well as issues of intensification of the grinding process by changing the surface profile of the armor plates are given. 1 Introduction The problem of energy saving in grinding of solid materials of natural and man-made origin is very relevant1 Calculation for Volume of Cement Slurry. To calculate the amount (sacks) of cement required for this surface casing cementing job, you need to know the kind of cement, density, and yield. For this example, we will utilize Class C Cement. The blend weighs 14.8 lb/gal, a Yield of 1.32 ft3/sk, and a Water Requirement of 6.3 gal/sk.Cementing Calculations- 7 Steps & Spreadsheets Drilling
احصل على السعر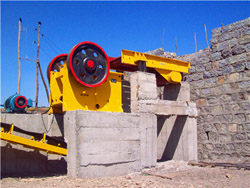
Cement Manufacturing Process Phases Flow Chart Cement
Cement Manufacturing Process Phase 1: Raw Material Extraction. Cement uses raw materials that cover calcium, silicon, iron and aluminum. Such raw materials are limestone, clay and sand. Limestone is for calcium. It is combined with much smaller proportions of sand and clay. Sand & clay fulfill the need of silicon, iron and This research focused the role to study the effects and ways to control the chemical composition of clinker for better cement production. Cement is a substance produced by grinding a mixture of aEffect of Free Lime and Lime Saturation Factor on Grindability of
احصل على السعر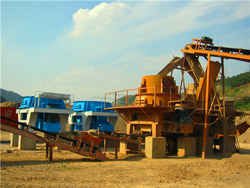
Cements ground in the vertical roller mill fulfil the quality
Cement process requires fine grinding of a material blend hence recent studies have been focusing on the improvements in these were considered and necessary calculations had been performed.
احصل على السعر- الصين مبيعات معدات معالجة المعادن الذهب
- 100 tph capacity of a stone crusher made in russia plant
- مطاحن الكرة تايوان
- حيث لشراء قضبان مطحنة الكرة طحن
- مطحنة حجر كربونات الصوديوم
- overall mining and stone crushers crusher for sale
- إندونيسيا آلة طحن
- لفصل المعادن من الفحم كسارة الفك
- مكائن استرداد الفضة المركزة
- mining machine 910 x 750 x 990
- مطحنة الكرة الجيرية المستخدمة على نطاق واسع
- مطحنة الكرة المحمولة في أسعار معالجة خام الذهب
- حجر كسارة آلة جيلي صانع
- environmental impact of coal 150tph mining in nigeria
- مطاحن عالمية عمودية مستعملة للبيع قوائم