اتصل
هاتف
+0086-371-86162511
عنوان
تشنغتشو ، الصين
mill power efficiency calculation

Modelling SAG milling power and specific energy
Tracking the mill performance showed that the mill power consumption decreased from 9.49 to 6.63 kWh/t (a nearly 30% reduction), P 80 of the mill product The mill energy as a function of time was obtained by multiplying the mill power by the mill volume and milling time. The milling efficiency, η, was calculated using Novel methodology for mill efficiency determination based
احصل على السعر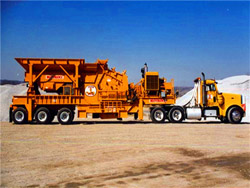
Grinding Mill Computer Model AusIMM
2. Metallurgical Power Requirements These are the equations based on the work by Bond and Rowland with autogenous power requirement based on the work In general, the milling media should fulfill two major requirements: (i) they should have large surface area to provide suitable contact with the material being milled; and (ii) they Milling Energy an overview ScienceDirect Topics
احصل على السعر
8VLQJ$VSHQ 3OXV6LPXODWRU IOPscience
the raw mill studied using Aspen plus simulator modelling technique was found to be 21.4%. It was found that the difference in exergy efficiencies of the simulation results of the three 14 May 2020 In previous publications, we have described how the size specific energy (SSE) can be calculated to predict the energy required to generate new minus 75 µm material. However, if we want to Quantifying the energy efficiency of fine grinding
احصل على السعر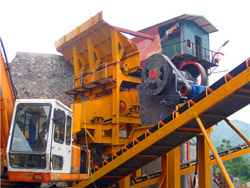
The Power Consumption Calculation of a Ball Drum Mill
discussed in this study based on the analysis of the mills where:N power to the output shaft of the gearbox;, with cross-longitudinal movement of the grinding media. The relative specific energy efficiency ratio is inversely proportional to specific grinding parameters and ground product particle sizes. The relative specific Studying the effect of different operation parameters on the
احصل على السعر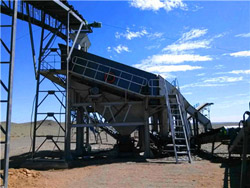
Novel methodology for mill efficiency determination based
The milling efficiency, η, was calculated using Equation 14 where SE T, is the total strain energy and Em, is the mill energy. Although using the mill energy similar to a stirred-tank underestimate the true mill energy due to the difference in the moving mass inside the mill from the stirred tank, it does not represent a main concern as theThis distribution affects the SAG mill load and the load affects directly the mill power and the efficiency of the mill operation (Van Nierop and Moys, 2001). If a SAG mill has been designed with a conventional power or specific energy model which do not consider the projected feed size distribution it is likely that this mill will reach theModelling SAG milling power and specific energy
احصل على السعر
(PDF) Toward a Simple Approach Determining
The calculations of the “phantom ” ball mill specific energy requirement (kWh/t) inside the SSSAG mill is based on recommendations put forth by Rowland (1978). Rowla nd (1978) recommends usingThe energy consumption of the total grinding plant can be reduced by 20–30 % for cement clinker and 30–40 % for other raw materials. The overall grinding circuit efficiency and stability are improved. The maintenance cost of the ball mill is reduced as the lifetime of grinding media and partition grates is extended. 2.5.Energy-Efficient Technologies in Cement Grinding IntechOpen
احصل على السعر
(PDF) Energy Efficiency Analysis of the Refining Unit in
Energy Efficiency Analysis of the Refining Unit in Thermo-Mechanical Pulp Mill. March 2021; This model is utilized to predict two essential variables for refining energy efficiency calculationThe energy savings has been attributed to higher energy efficiency of the HPGR at low reduction ratios, smaller particle top sizes in the ball mill feed, and the weakening of particles resulting(PDF) Effects of Ball Size Distribution and Mill Speed and
احصل على السعر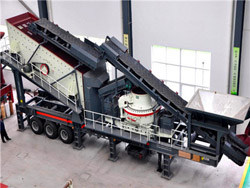
Actual SAG Mill Operating Power Download Table
The SAG mill power draw model of Austin (using the calibration by Doll, 2013) is used to predict the process power draw at the mill shell, P shell,and the efficiency losses for the drive'sand tandem mill speed on 1) the extraction of sugar from sugar cane, 2) power requirements in the mill, 3) specific energy consumption in the mill, 4) specific extraction per energy consumption in the mill. 2 Materials and methods 2.1 Equipment used in the test Testing was performed using a small milling machine (Figure 1) with two tandem millsOptimization of milling performance of a sugar mill
احصل على السعر
Energies Free Full-Text Energy Efficiency Analysis of the
A refining model is developed to analyses the refining process’s energy efficiency based on the refining variables. A simulation model is obtained for longer-term refining energy analysis by further developing the MATLAB Thermo-Mechanical Pulping Simulink toolbox. This model is utilized to predict two essential variables for refining Furthermore, the power consumption of the raw mill grinding process was reduced by 6.7 percent by using exterior hot gas, as suggested in an energy and exergy analysis of the mill by Atmaca(PDF) Thermodynamic Analysis of Raw Mill in Cement
احصل على السعر
6-2 Energy Optimization TAPPI
The third key factor in mill energy efficiency is the steam power balance. Nearly all kraft mills employ steam turbine generators to produce electricity and low and . 6.2-3 medium pressure process steam. However, many mills have not fully optimized the potential power generationThe process of ball milling and the materials that compose planetary ball mills are highly complex, and the existing research on the change in ball-milling energy is not mature. The theoretical model of a Model Study of Mechanicochemical Degradation
احصل على السعر
Energy performance comparisons and enhancements in the
In this study, energy-related operational parameters for modern and traditional (conventional) sugar mills are analyzed, with the goals of identifying improvements in energy efficiency and potential for surplus electricity export. Results show that the power-to-heat ratio of modern and traditional mills is clearly distinct, lying in the In this example, the OWi of the SAG mill was found to be 30% higher than the ball mill, thus suggesting that the SAG mill was less efficient than the ball mill. As referred to earlier, the size-specific energy calculation has typically been conducted at a marker size of 75 µm 5,6,7Quantifying the energy efficiency of fine grinding circuits
احصل على السعر
Wind Power The Engineering ToolBox
The actual available power from a wind mill with diameter 1 m,efficiency 0.2 (20%) with wind velocity 10 m/s can be calculated as. P a = (0.2) (1.2 kg free apps for offline use on mobile devices. Online Wind Power Calculator. The calculator below can be used to calculate the available power from a windmill: ρ density of air (kg/m@article{osti_922135, title = {Improving Energy Efficiency Via Optimized Charge Motion and Slurry Flow in Plant Scale Sag Mills}, author = {Rajamani, Raj K}, abstractNote = {A research team from the University of Utah is working to make inroads into saving energy in these SAG mills. In 2003, Industries of the Future Program of the Improving Energy Efficiency Via Optimized Charge Motion
احصل على السعر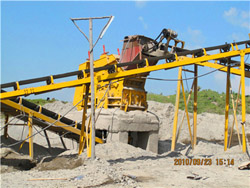
Quantifying Grinding Efficiency 911 Metallurgist
2 天之前You perform size analysis of the different streams and then calculate the grinding efficiency and classification efficiency. Make sure that every sampling campaign last at least 4 hours to make sure that the circuit is in steady state. Mill power as measured in many plants is motor input power, that is, electrical energy going into theThe energy efficiency of the furnace is 71.01%, while exergy efficiency is 51.41%, indicating a potential for energy-saving improvements of the present furnace.Analysis on energy consumption and performance of
احصل على السعر
Milling Energy an overview ScienceDirect Topics
Hardness—the hardness of a powder material is considered to be the most important characteristic to realize when deciding on what type of milling media to choose.The harder the milling media the better the milling efficiency. Using milling media made of hard materials such as hardened steel, tungsten carbide, agate, and zirconia leads to maximize the This study evaluates the technical potential of mild hydrothermal carbonization (HTC) at 160 °C for 3 h to improve the energy efficiency of on-site incineration as a biosludge handling method.(PDF) Improving Kraft Pulp Mill Energy Efficiency through
احصل على السعر- تايلند سعر الفحم الحراري
- كسارة الفحم نقلت
- تركيب الغسالة الفوق اتوماتيك
- portable crusher plant india
- بيع معدات مناولة المواد للفحم
- وحدات معالجة الباريت في السعودية
- خطط آلة التصنيع باستخدام الحاسب الآلي قوات الدفاع الشعبي
- plant de concassage mobile
- خط انتاج المعجون
- كيفية طحن البازلت
- الشركة المصنعة لإنتاج النحاس
- Low Price Professional Sand Rotary Dryer Manufacturer For Sale
- كسارة الجرانيت المدمجة كسارة خام كسارة خام
- سعر كسارة الحجر شنغهاي
- عدد طواحين الانسان