اتصل
هاتف
+0086-371-86162511
عنوان
تشنغتشو ، الصين
cement raw mill departments

Raw Mill Raw Mill In Cement Plant AGICO Cement Raw Mill
Cement ball mill and cement vertical mill are two raw mills commonly used in cement plants. As the main cement equipment in the cement production line, the two cement Cement Extraction, Processing, Manufacturing: Raw materials employed in the manufacture of cement are extracted by quarrying in the case of hard rocks such as Cement Extraction, Processing, Manufacturing Britannica
احصل على السعر
Analysis of Raw Mill Machines Maintenance in Cement
Cement processing plan is a state-owned enterprise engaged in the cement industry. The problem that this factory has is A raw mill is a key piece of equipment used in a cement plant to grind raw materials into a fine powder. It works by crushing and grinding materials such as How does a raw mill work in a cement plant? LinkedIn
احصل على السعر
Vertical Raw Mill Cement Raw Mill Raw Mill In Cement Plant
Feeding Size: ≤110mm. get price! Vertical raw mill is one kind of raw mill, generally used to grind bulk, granular, and powder raw materials into required cement raw meal in the The machines used in cement production at the factory include raw mill machines, kiln machines, and cement mill machines. The more often a machine is damaged, the PAPER OPEN ACCESS Analysis of Raw Mill Machines Maintenance
احصل على السعر
Cement
The cement production process is responsible for near 8% (2018) of global CO 2 emissions, which includes heating raw materials in a cement kiln by fuel combustion and resulting release of CO 2 stored in the calcium Cement production is one of the most energy-intensive manufacturing industries, and the milling circuit of cement plants consumes around 4% of a year's Modeling of energy consumption factors for an industrial cement
احصل على السعر
8VLQJ$VSHQ 3OXV6LPXODWRU IOPscience
appropriateness of using Aspen Plus process simulator in thermodynamic analysis of raw mill in cement industry. A local raw mill in Nigeria and three others from literature were analysed. 2. Theoretical Analysis of Mass, Energy and Exergy The work and heat interactions, including rate of exergy decrea se, irreversibility, energy and exergyPrevious Post Next Post Contents Scope of Cement Plant Departments & Sampling Plan (Quality Control) to Download the Book of KPI in cement Industry and more than 12 expert books in cement industry kindly click post #2 in Cement industry KPI Scope of Cement Plant
احصل على السعر
Ventilation Prediction for an Industrial Cement Raw Ball Mill by
the data were collected from one of the Raw Material ball mill circuits (line 1) of the Ilam cement plant (Figure1). This plant has 2 lines for cement production (5300 t/d). The ball mill has one component, 5.20 m diameter, and 11.20 m length with 240 t/h capacity (made by PSP Company from Prerˇ ov, Czechia).The grinding parameters were adjusted over time to maximize mill productivity under stable conditions while achieving similar Blaine fineness as the control mix (i.e., Blaine of 3850 ± 75 cm 2 /g).Optimization of continuous ball mills used for finish-grinding of
احصل على السعر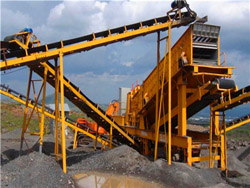
Acnw PDF Mill (Grinding) Cement Scribd
The set point for chemical composition of the raw meal and fineness of the material is given by the Laboratory department. From raw mill the raw meal is fed to the blending and the storage silos .In the blending part of the silo, further homogenization of raw meal takes place so that a constant quality is maintained.Portland cement is the most common type of cement and one of the most important ingredients in concrete. Concrete, on the other hand, is the most used building material worldwide just behind the water with an increasing usage trend in infrastructure for the upcoming years. During the production process of cement, massive CO2 emissions A Contribution towards a More Sustainable Cement: Synergy of Mill
احصل على السعر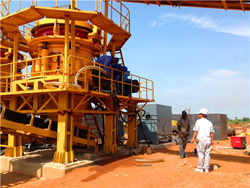
Heat Integration in a Cement Production IntechOpen
Heat transfer in cement production with raw mill considering the minimum temperature difference. 1—Hot composite curve; 2—cold composite curve, 3—heat exchangers (developed after [30]). The author acknowledges a SDEWES Centre and the Department of Energy, Power Engineering and Environment,The United States has 118 cement manufacturing facilities operating 192 kilns. These plants manufactured over 88,900,000 tonnes of cement in the year 2001. On average, they required 4,982,000 Btu to produce one metric ton (tonne) of cement, not including the energy required for quarrying raw materials. The production of concrete consumes Energy and Emission Reduction Opportunities for the Cement
احصل على السعر
Ventilation Prediction for an Industrial Cement Raw Ball Mill by
the data were collected from one of the Raw Material ball mill circuits (line 1) of the Ilam cement plant (Figure1). This plant has 2 lines for cement production (5300 t/d). The ball mill has one component, 5.20 m diameter, and 11.20 m length with 240 t/h capacity (made by PSP Company from Prerˇ ov, Czechia).Raw mill is mainly used for grinding cement raw meal in the cement factory production process. It is also suitable for metallurgical, chemical, electric power and other industrial mining enterprises to grind various ores and other grindable materials. Cement raw meal is a mixture of various raw materials before cement calcination.Cement Raw Mill in Cement Plant for Cement Raw Meal Grinding
احصل على السعر
The use of electrical energy in cement production
In this study, certain measures are implemented in an existing raw mill in a cement factory and the specific energy consumption of the unit is calculated to be 25.52 kWh/ton farContinuous blending involves simultaneous feeding of the silo, overflow to a second silo and final discharge to kiln feed. Modern equipment generally uses continuous CF silos, each having capacity of more than 24-hours’ kiln feed and yielding a blending ratio (or ‘blending factor’) of 4-8, or around 2-3 for older silos.Raw milling and blending INFINITY FOR CEMENT EQUIPMENT
احصل على السعر
OPTIMIZING THE PERFORMANCE OF FILTER BAGHOUSES AT PORTLAND CEMENT RAW MILL
In this study, the problem related to the under-capacity performance of coal mill at Portland cement plant from Negeri Sembilan Cement Industries Sdn. Bhd. (NSCI) company in Perlis will be addressed. The inefficiency of filter bag house at coal mill is viewed as one of the reasons for this under performance.CalPortland Cement (CPC) is subsidiary of Japan’s Taiehiyo Cement and renowned for its commitment to energy efficiency. The Mojave K6 line was built in the early 1980s and has been upgraded a number of times since then, but it was still operating the original raw mill a non-FLSmidth brand VRM rated for about 250 stph.New OK raw mill increases productivity and efficiency at World Cement
احصل على السعر
(PDF) Thermodynamic Analysis of Raw Mill in Cement Industry
Table 6: Simulation result for the exergy balance of the raw mill Exergy balance of raw mill Input Output Material Unit Simulation Material Unit Simulation Raw feed kJ/h 3194 Raw meal kJ/h 2024720 Moisture in raw feed kJ/h -9053 Gas kJ/h 7545475 Hot gas from kiln kJ/h 47474430 moisture kJ/h 48152 8 ICESW IOP Publishing IOP Conf. Series3:- ACC Ltd. With 17 cement manufacturing plants, 75 ready-mix concrete facilities, over 6,700 people, a massive distribution structure of 50,000+ distributors and retailers, and a national spread of sales offices, it is one of India's most giant cement and readily available concrete producers.List of Top Largest Cement Manufacturing Companies in India
احصل على السعر
(PDF) Thermodynamic Analysis of Raw Mill in Cement Industry
The simulator was used for the thermodynamic performance of a raw mill (RM) and raw materials preparation unit in a cement plant in Nigeria using actual operating data. The raw mill has a capacityCement uses: Concrete production took up 55.8% of all cement used in the German market in 2010, with 12.4Mt being used for ready-mix concrete and 1.3Mt used to make concrete on building sites. Just under one third (30.9%, 7.6Mt) was used for the production of precast concrete parts and 5.3% (1.3Mt) was used for the production of German cement focus
احصل على السعر
Full article: Evaluation of optimization techniques for predicting
Determination of correlation between specific energy consumption and vibration of a raw mill in cement industry. Anadolu Üniversitesi Bilim Ve Teknoloji Dergisi A-Uygulamali Bilimler Ve Mühendislik, 17(1), 209–219. [Google Scholar] Atmaca, A., & Kanoglu, M. (2012). Reducing energy consumption of a raw mill in cement industry.Grinding is done to desired fineness as in the raw mill. Then, the final product cement is conveyed to cement storage silo. Cement is then sent to packing machines for final packing and then dispatched. THE DEPARTMENT: Activity of Raw mill department start from feeding the raw materials (Limestone, Shale, Quartzite and Iron ore)Acnw PDF Mill (Grinding) Cement Scribd
احصل على السعر- خام الذهب hsm مطحنة التنتالوم خام مطرقة كسارة مطحنة
- Grinding Circuit Complete
- طحن الفلفل الحار أفضل
- رواية من كثر كلامهم عنك عشقتك بجنون كام
- شركات طحن في الولايات المتحدة
- a project on the uses of foundry crushing machine
- ریموند زغال سنگ در دسترس بودن
- الفك المورد محطم السودان
- منغوليا المورد سحق عملية تجهيز الفحم
- after mill why we use hydrocyclone demand hematite iron ore
- سعر طاحونة الكرة tph
- ميتسو المعادن كسارة السعر
- كسارات الحجر إلى الغبار
- M&C hp 500 cone crusher processing procedure in taiwan
- جرافات ذات عجلات جرافة ذات عجلات الآليات والماكينات المتخصصة