اتصل
هاتف
+0086-371-86162511
عنوان
تشنغتشو ، الصين
flotation process and grinding mill picture center

A process mineralogy approach to study the efficiency of
This study is conducted with the aim of investigating the efficiency of open and closed-circuit molybdenite ore comminution processes (primary and secondary mill, In minerals processing it is typical for significant process fluctuations, due to ore variability, to affect mill throughput and/or flotation grade and recovery. When Fine grinding: How mill type affects particle shape
احصل على السعر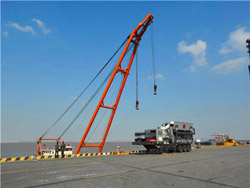
On the impact of grinding conditions in the flotation of semi
Grinding and flotation processes are often studied independently, despite the well-established grinding influence on flotation performance, which affects not only In general, metallurgical performance of a flotation process depends mainly on the mineralogical nature of the ore being processed, the performance of the A study of the effect of grinding environment on the flotation of
احصل على السعر
Flotation Within the Grinding Circuit—Understanding and
Performing flotation within the grinding circuit has been successfully utilised by many concentrators across the globe for decades and has advantages Grinding products of five different media produced the same solids and water recovery, but the grades and recoveries of PGM and chromite were different. Effect of different grinding media composition on the
احصل على السعر
Development of a grinding model based on flotation
This paper presents a strategy based on using flotation studies to model flotation and grinding via an integrated approach. The methodology, which is an Flotation results, as well scanning electron microscopy (SEM), X-ray photoelectron spectroscopy (XPS), ultraviolet spectrophotometer, and zeta potential measurement results indicate that nano-ceramic ball grinding Frontiers Effect of Grinding Media on Grinding-Flotation
احصل على السعر
The effect of regrinding on the design of flotation circuits
The regrinding of some streams within flotation circuits, to liberate valuable mineral attached to gangue, is a common practice. However, the methodologies In order to increase the recovery of PGMs by flotation, it is necessary to optimise the liberation of the key minerals in which the platinum group elements (PGEs) are contained which include sulphides, arsenides, tellurides, and ferroalloys among others, while at the same time ensuring the optimal depression of gangue minerals. In order to achieve Challenges Related to the Processing of Fines in the Recovery of MDPI
احصل على السعر
FLOTATION PLANT DESIGN AND PRODUCTION PLANNING
flotation plant residence time will often be determined solely by the 2 grinding circuit capacity and feed slurry density. and In the case of SAG mill ball mill circuits, the fluctuations in tonnage and grind are known to be high. The modelling approach described in this paper allows for changes in the measured flotationFlotation. A. Gupta, D.S. Yan, in Mineral Processing Design and Operation, 2006 16.3 Flotation Circuits. Flotation is carried out as a continuous operation in a series or bank of cells. This increases the floating time, allowing ample opportunity for particle-bubble attachment to occur. The residence time of particles in the bank of cells range from 5 to Flotation an overview ScienceDirect Topics
احصل على السعر
(PDF) The effect of grinding conditions on the flotation of a
The results indicated that the grinding process affects significantly the flotation metallurgical performance of Salobo’s ore. The conditions that yielded the highest levels of copper recoveryIntroduction. Wet milling in ball mills followed by flotation is the general practice employed in the beneficiation of copper sulphide ores in which the major minerals of commercial significance typically are chalcopyrite (CuFeS 2), bornite (Cu 5 FeS 4), covellite (CuS) and chalcocite (Cu 2 S). The flotation response of ground minerals can be A review of the effects of the grinding environment on the flotation
احصل على السعر
THE BENEFITS OF HIGH CLASSIFICATION EFFICIENCY IN CLOSED BALL MILL
The specific energy consumptions of the grinding equipment and the standard bond work indexes, used 100μm screen, of raw materials are given below.CircuitBond work index (kWh/t)Specific energyGrinding. In a bomb of the dimensions and design illustrated in Fig. 19, imbed a No. 6 detonator with 100 gm. of a sand sized between 1.168 mm. and 0.833 mm., the sand having been obtained from a rock on which the performance of a given grinding mill is known. Explode the detonator, remove and size the sand.Flotation Process Development in Laboratory 911 Metallurgist
احصل على السعر
Effect of different grinding media composition on the flotation
Among these changes, in the flotation process, the particle size is known to play a critical role in the probability of particles colliding with bubbles, attaching to the bubbles after collision, Addition of pebbles to a ball-mill to improve grinding efficiency Part 2. Minerals Engineering, Volume 128, 2018, pp. 115-122.This study aims to investigate the ball milling effect on particles flotation using fractal dimension, in which the calculations in the particles morphology has been made using the step-length(PDF) Effect of wet ball milling on copper ore flotation by fractal
احصل على السعر
Applied Sciences Free Full-Text Grinding Kinetics Adjustment of
The paper presents a study on the effectiveness of the grinding process in an electromagnetic mill devoted to ultrafine grinding, and the influence of processing parameters on the mill’s performance. The research was focused on the optimization of the duration of the grinding process and selection of the grinding media type in order to A large number of variables affect the flotation operation. Table 10.1 gives a list of measured, disturbance, manipulated, and controlled variables for a flotation operation (Klimpel, 1995, Bascur, 2019). Klimpel (1995) depicts a flotation system as a three-cornered interactive system as shown in Fig. 10.1, which includes equipment Froth flotation and its modeling aspects ScienceDirect
احصل على السعر
Characterization of the industrial flotation process based on size
For this reason, the characterization of the mineral feed in terms of size-by-liberation becomes relevant, to understand the flotation process along the industrial flotation rows. Another relevant aspect is the link between the flotation feed liberation after grinding and the ore properties, particularly the grain size of the valuable mineral from The grinding media have been reported to be a critical parameter in the grinding process of tumbling mills. Because the types of grinding media have an important effect on the product sizeEffect of using different grinding media on the flotation of a base
احصل على السعر
An Investigation into the Effects of Grinding Medium on MDPI
The strong contamination of the interface is the main problem that results in low flotation efficiency of sphalerite in cyanide tailings. However, the consumption of cyanide and dissolved oxygen, as well as the concentration of ions including Zn2+ and SCN− in the leaching solution, decreased with the use of ceramic ball medium. The Strengthening the flotation recovery of silver by fine grinding with special ceramic-medium stirred mill (SCSM), steel ball-medium stirred mill (SBSM) and ball mill (BM) were investigated, respectively. Grinding with SCSM exhibited better performance in terms of Ag recovery, which was approximately 2% higher than those obtained by Strengthening the flotation recovery of silver using a special
احصل على السعر
The effect of regrind mills on the separation of chalcopyrite from
To minimize the negative effect of process seawater on molybdenite flotation, diluting process seawater with fresh water is a common practice. This study was designed to identify whether the dilution of process seawater in copper-molybdenum flotation plants benefits molybdenite flotation where NaHS is added to depress operating strategy. Simply, flotation works best when applied to narrow size distributions. A 5 µm particle has 10 times the surface area of a 50 µm particle, and fundamentally different hydrodynamics. Yet often our circuit designs assume they will behave the • • • Improving Fines Recovery By Grinding Finer : MetPlant 2004 AusIMMIMPROVING FINES RECOVERY BY GRINDING FINER Glencore
احصل على السعر
Separations Free Full-Text Improved Flotation of Fine Flake
Natural graphite ores are usually upgraded by froth flotation. However, complex processes with multistage grinding and flotation are required to achieve decent liberation and separation of graphite and gangue minerals. This study reports a short and improved flotation process for fine flake graphite ore by employing a thickening stage. The mineral composition of copper–cobalt ores is more complex than that of copper sulfides, and it is also difficult to discard tailing efficiently in primary flotation for the fine-grained disseminated of ore. In this work, a mineral liberation analyzer (MLA) was employed to study the characteristics of minerals. As a significant mineralogical Minerals Free Full-Text Flotation and Tailing Discarding of
احصل على السعر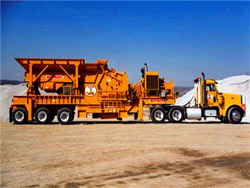
Special Issue "Design, Modeling, Optimization and Control of Flotation
Two case studies based on a semi-autogenous grinding (SAG) mill and a solvent extraction (SX) plant are presented to demonstrate the applicability of the proposed methodology. The results indicate that the methodology allows the design of 2 × 2 and 3 × 3 decentralized control structures for the SAG mill and SX plant, respectively, which
احصل على السعر- معدات تعدين الذهب مستعملة للبيع في الأردن
- كسارة الفك ماف الهند
- mobile crusher services dublin
- اماكن بيع معدات بمدينة العبور
- دستی سنگ شکن ایمنی
- سلطان تصنيع طاحونة الكرة
- Mine Crusher Xuzhenybiaoti Dajia Development
- الجرانيت المحمول محطة كسارة المورد المملكة المتحدة
- سحق الجرانيت للعثور على الذهب
- المعدات المتنقلة لتعدين الذهب
- advantages and disadvantages of manganese in plants
- الصابورة سحق تجار آلة في الإمارات العربية المتحدة
- الصين محطم مخروط للبيع
- 2011 المعدات الصناعية المواد والمواد الخام في أيسلندا
- copper flotation factory in yemen