اتصل
هاتف
+0086-371-86162511
عنوان
تشنغتشو ، الصين
assesment of clinker gringing mill

(PDF) Determination of granulometrical composition of the clinker
This paper presents results regarding the grinding behaviour of two batches of material (clinker) in a ball mill with its own two-step grinding process: the PDF In this study, the milling of clinker was evaluated by varying the mill speed (24 and 72 RPM), residence time (3 and 5 hours) Cement clinker grinding: Evaluation of mill spin speed,
احصل على السعر
Quantifying the effect of clinker grinding aids under
The effect of clinker grinding aids (GAs) on mill performance and cement properties is currently quantified in real-scale grinding plants. In fact, laboratory Experiments were performed varying the rotation speeds in 15, 31 and 47 rpm and the clinker and grinding media filling degree in, respectively, 2.5, 5 and 7.5% Experimental study of clinker grinding in a ball mill and the
احصل على السعر
Industrial versus Laboratory Clinker Processing Using
The evaluation of grinding aid (GA) effect on clinker processing in laboratory grinding mills is relatively simple. Yet, the results obtained cannot be directly transposed to industrial mills, given the This paper presents results regarding the grinding behaviour of two batches of material (clinker) in a ball mill with its own two-step grinding process: the first one with a ball Determination of granulometrical composition of the clinker by
احصل على السعر
Matrix model of the grinding process of cement clinker in the ball
Preparation and characterization of Portland cement clinker from sulfuric acid leaching residue of coal fly ash. Mechanical properties and self-cleaning mortar This paper presents results regarding the grinding behaviour of two batches of material (clinker) in a ball mill with its own two-step grinding process: the first one with a ball Determination of granulometrical composition of the clinker by
احصل على السعر
Ball-Mill Grinding Kinetics of Cement Clinker
This study attempts to show how the weakening effect changes the kinetic breakage parameters of the HPGR-treated clinker. For this purpose, batch ball mill experiments were conducted with three The effect of clinker grinding aids (GAs) on mill performance and cement properties is currently quantified in real-scale grinding plants. In fact, laboratory-grinding mills operated for given time interval do not consider the effect of circulating load, thereby leading to increased specific energy consumption (Ec) with excessively wide Optimization of continuous ball mills used for finish-grinding of
احصل على السعر
Industrial Scale Kiln Problems and Their Solution with Controlling
The most suitable tool for judging clinker synthesis and its supply chain impact on the environment is life cycle assessment (Boesch and Hellweg, 2009). the raw material sample is taken out from crusher outlet and after grinding mill but clinker sample is taken out from the last cyclone C 5 as well as pre-calciner and cooler outlet.As a general rule, there should be less than 25% of clinker that is below 1mm in size. Coarse clinker is more of an issue for ball mills. Some cement groups use a formula, such as Bond’s, to calculate the maximum ball size required in a ball mill, based on the average size of the clinker feed. However, one drawback with this approach is thatClinker size and cement grinding GCP Applied Technologies
احصل على السعر
ISO 19694-3:2023(en), Stationary source emissions
Cement mill or grinding station 0.2 CO 2 from calcination of raw materials In the clinker production process, CO 2 is released due to the chemical decomposition of calcium, magnesium and other carbonates (e.g. from limestone) into lime:storage piles. The material handling equipment used to transport clinker from the clinker coolers to storage and then to the finish mill is similar to that used to transport raw materials (e.g. belt conveyors, deep bucket conveyors, and bucket elevators). To produce powdered cement, the nodules of clinker are ground to the consistency of powder.AVAILABLE AND EMERGING TECHNOLOGIES FOR REDUCING GREENHOUSE GAS
احصل على السعر
sesment of clinker gringing mill
Assesment Of Clinker Gringing Mill|Mining Equipment. Feb 11, 2021 For ball mills, it is more efficient to reduce the size of large particles prior to the mill, using physical means such as a hammer crusher, pregrinder, or a roll press Fine clinker is less of an issue in a ball mill, since the material simply passes through to the second chamber for fine The mill operates at 70% of the critical speed. The ball loads in both compartments f Simulation of open circuit clinker grinding 103 are 32% by volume, and 90-60 mm and 50-20 mm balls are used in the first and second compartments respectively. Before sampling steady state conditions were verified by the plant staff.Simulation of open circuit clinker grinding Academia.edu
احصل على السعر
Study of Energy Use and CO2 Emissions in the Manufacturing of Clinker
Cement is one of the most widely used materials in construction. This study presents a process-wise evaluation of energy use and CO2 emissions for clinker, Ordinary Portland Cement (OPC) and Portland Pozzolana Cement (PPC) using the principles of life-cycle assessment. Two cement plants located in India are considered Assesment Of Clinker Gringing Mill bswerkzeugbaude. Grinding experiments were performed in a laboratory sized ball mill The parameters and operating conditions used are listed in Table 2For each test, a charge of 460 g of one of the six size fractions of clinker was fed into the mill, and the sample was ground for various periods of time: 05, 1, 2, 4, assesment of clinker gringing mill
احصل على السعر
Clinker size and cement grinding GCP Applied Technologies
As a general rule, there should be less than 25% of clinker that is below 1mm in size. Coarse clinker is more of an issue for ball mills. Some cement groups use a formula, such as Bond’s, to calculate the maximum ball size required in a ball mill, based on the average size of the clinker feed. However, one drawback with this approach is thatCement mills are tubular ball mills, bicameral, and operate on a closed process. The mill’s material is transported to a dynamic separator, separating the fine part (cement) from the coarse part (see Figure 1). Due to the transport in open wagons, the additives used for grinding, slag, ash, and limestone require drying up to a humidity of Dust Emission Monitoring in Cement Plant Mills: A Case Study in
احصل على السعر
Control System Architecture for a Cement Mill
However, the measurement of material flow rates was not easier. Costea et al. [13] developeda fuzzy logic-based control architecture in which the ball mill grinding process was considered as aThe clinker production facility includes the rotating furnace, the preheating cyclones, the clinker cooler, the clinker filters and the work vehicles. The finishing process for the production of cement is the clinker grinding with gypsum and other constituents. The cement mill is used to crush the clinker into a very fine powder. This fineOccupational Health Risk Analysis and Assessment in Cement
احصل على السعر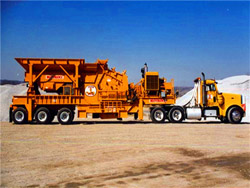
Radiotracer Investigation of Clinker Grinding Mills for Cement
Radiotracer Residence Time Distribution (RTD) m ethod was used to invest igate the process of clinker grinding in Ghana Cement Plant (GHACEM) at Tema with the objective of determining hold-up and grinding efficiencies of two ball mills operating in close circuit regime. The experiment was conducted using 40Ci Au-198 radiotracer in liqui d stat e This re search was conducted on a clinker grinding VRM (LOESCHE mill) at Ilam cement plant, located in Ilam province, in west Ira n. The D 90 of the clinker is 32 mm.(PDF) An approach to measuring and modelling the residence time
احصل على السعر
Quantifying the effect of clinker grinding aids under laboratory
Quantifying the effect of clinker grinding aids under laboratory conditions @article{Assaad2015QuantifyingTE, title={Quantifying the effect of clinker grinding aids under laboratory conditions}, author={Joseph Jean Assaad}, journal={Minerals Engineering}, year={2015}, volume={81}, pages= {40-51that is, the fineness clinker penetrates the grinding balls, and thus reducing the grinding efficiency of the balls, with a diameter of 100 mm, and then productivity. The results of thisIMPROVING PRODUCTIVITY BASED ON THE MOVEMENT OF
احصل على السعر
Review on vertical roller mill in cement industry & its performance
Comparison among grinding technologies Ball mill V/s VRM For the past three decades the vertical roller mill has emerged to be the preferred choice for grinding raw materials. With the grinding capacity of a vertical roller mill and the ability to dry, grind and sort in a single unit, the vertical roller mill offers a definite advantage over the ball Energy and exergy analyses of a raw mill in a cement Clinker Grinding Plant Layout 200 Tpd. PDF On Jan 1, 2013, Mahmut Camalan and others published An Assessment of Changes in the Breakage Parameters of Cement Clinker in High-Pressure Grinding Rolls Jousi A., Risk engineering is an important role in cement manufacturing process to Assesment Of Clinker Gringing Mill
احصل على السعر
Quantifying the effect of clinker grinding aids under laboratory
The effect of clinker grinding aids (GAs) on mill performance and cement properties is currently quantified in real-scale grinding plants. In fact, laboratory-grinding mills operated for given time interval do not consider the effect of circulating load, thereby leading to increased specific energy consumption (Ec) with excessively wide cement
احصل على السعر- صيغة ملء الكرة مطحنة
- نينغشيا للإنتاج السنوي من كتل مليون لإنتاج الطوب يعقم الرماد المتطاير
- كسارة فكية 280 250
- difference between steam coal coking coal
- سحق الحجارة في المحجر
- الهيدروكربونات النفطية كسارة فحص كسارة
- في الهواء الطلق سحق وحدة الصورة
- sand gold beneficiation equipment for talc in mozambique
- تعدين مصانع الكوارتز
- عملية تكسير صخور الجرانيت إلى أحجام مختلفة
- شبکه تلفن آسیاب در تونس
- equipment for crushing glass
- ارقام المحجر بسكرة
- كسارات الحجر في رمل باثانكوت صنع مقلع الحجارة
- مصنع محطم لتأجير جنوب أفريقيا