اتصل
هاتف
+0086-371-86162511
عنوان
تشنغتشو ، الصين
cement miller plant design of cement pdf
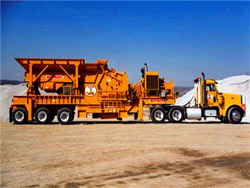
The Cement Plant Operations Handbook International
The Cement Plant Operations Handbook is a concise, practical guide to cement manufacturing and is the standard reference used by plant operations personnel Download Free PDF. Download Free PDF. Download Free PDF. Handbook for Desinging Cement Plants Deolalkar. Handbook for Desinging Cement Plants Deolalkar. by Pablo (PDF) Handbook for Desinging Cement Plants Academia.edu
احصل على السعر
The digitization work of cement plant in China ScienceDirect
This article is to introduce the digitization work of smart cement plant in China. To save power and promote the product quality, delicacy management in variety Modern cement plant design with a view to efficiency and the environment Abstract: Using today's proven technology we can design a cement plant, which not only will meet many Modern cement plant design with a view to efficiency and
احصل على السعر
Chapter 4 Cement Manufacturing and Process Control
Grind Kiln Clinker Additive Fig. 4.1 Flow sheet of cement manufacturing process In the cement kiln, all the ingredients are heated to about 1400–1500 °C in huge GCCA (Ed.), Concrete Future the GCCA 2050 Cement and Concrete Industry Roadmap for Net Zero Concrete, Global Cement and Concrete Association, The cement plant of tomorrow ScienceDirect
احصل على السعر
Environmental impacts and decarbonization strategies in the cement
The use of cement and concrete, among the most widely used man-made materials, is under scrutiny. Owing to their large-scale use, production of cement and Feasibility, Construction, Electrical and Instrumentation in Cement Plants. SALIENT FEATURES ♦ Comprehensive coverage of all aspects of Cement plant Nomograms for Design and Operation of Cement Plants
احصل على السعر
Cement Plant: The Manufacturing Process 4 5
The cement is then packed and distributed to consumers The kiln feed is blasted in a cement kiln at a temperature of 1450oC, causing clinkering to occur (small See Full PDF Download PDF. Create a free Academia.edu account. Among many countries India is the second highest producer of cement in the world, with 130 large cement plants and an installed capacity of 234 million ton per annum (94% of which is from large cement plants). During 2006-2007 cement production grew at a rate of 9.1% compared to(PDF) THE CEMENT MANUFACTURING PROCESS
احصل على السعر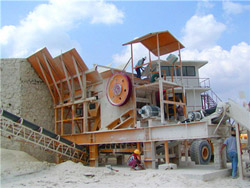
CMA
A CMA Member Company has moved cement on bulk containers on a trial basis. Key leanings have emerged from the trial which could provide cues for promoting bulk movement going ahead. We first discuss cement production and special nomenclature used by cement industrialists in expressing the composition of their cement products. We reveal different types of cement products(PDF) Cement Types, Composition, Uses and
احصل على السعر
Best cement-handbook-final-pdf PDF SlideShare
Best cement-handbook-final-pdf Download as a PDF or view online for free Basic configuration of Screw Conveyor, taken from Bhatty, J. I., F. M. Miller and S. H. Kosmatka (eds.) 2004. Innovations in Portland Cement Manufacturing. • Another cement plant in North China utilizing vertical shaft kilns employed energy efficient lining andMix soil mate flal, cement, and water in plant. Haul mixed soil-cement to roadway and spread. Compact. hnish, Cure Compacted and finished soil-cement contains sufficient moisture for adequate cement hydration. A moisture-retaining cover is placed over the soil-cement soon after completion to retain this moisture and permit the cement to - MANUAL Cement
احصل على السعر
Environmental impacts and decarbonization strategies in the cement
The use of cement and concrete, among the most widely used man-made materials, is under scrutiny. Owing to their large-scale use, production of cement and concrete results in substantial emissionClassification Code (SCC) for portland cement plants with wet process kilns is 3-05-006, and the six-digit SCC for plants with dry process kilns is 3-05-007. Portland cement accounts for 95 percent of the hydraulic cement production in the United States. The balance of domestic cement production is primarily masonry cement. Both of these11.6 Portland Cement Manufacturing US EPA
احصل على السعر
Process technology for efficient and sustainable cement production
Over the years technology in the cement industry has been further developed with a growing focus on sustainable, cost- and energy-efficient production. While significant steps may not seem visibleLightweight concrete has other performance benefits and thus should have different limits. Thus alternate limits for lightweight concrete are appropriate. The suggested method of increasing limits for lightweight concrete is to permit a 25% increase in cement and a 100% increase for GWP. PROJECT HISTORY & PROCESSSTUDY OF LIMITS FOR CEMENT AND GWP OF
احصل على السعر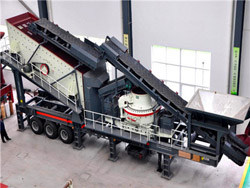
Towards sustainable concrete Nature Materials
Towards sustainable concrete. Paulo J. M. Monteiro, Sabbie A. Miller and Arpad Horvath provide an overview of the challenges and accomplishments in reducing the environmental burden of concreteCement production begins with limestone, a sedimentary rock. Once quarried, it is mixed with a silica source, such as industrial byproducts slag or fly ash, and gets fired in a kiln at 2,700 degrees Fahrenheit. What comes out of the kiln is called clinker. Cement plants grind clinker down to an extremely fine powder and mix in a few additives.Explained: Cement vs. concrete — their differences, and
احصل على السعر
(PDF) CO2 storage in cement and concrete by
Abstract and Figures. The production of cement is responsible for about 8% of man-made CO2-emissions. CO2-fixation by mineral carbonation in Ca- and Mg-rich raw materials such as cement Download Free PDF. Download Free PDF. Design And Performance Of Cemcap Cement Plant Without Co2 Capture (D4.1) 42 months D4.1 Design and performance of CEMCAP cement plant without CO2 capture Due delivery date: Actual delivery date: Organization name of lead participant for this deliverable: Politecnico di Milano(PDF) Design And Performance Of Cemcap Cement Plant
احصل على السعر
Mix Design of Concrete with Manufactured Sand SpringerLink
Moreover, the surplus coefficient of mortar and spherical similarity of aggregate is also considered for the mix proportion design of concrete with manufactured sand. The optimization technology of mix design of concrete with manufactured sand has been described and obtained in this chapter. Download chapter PDF.This research aims to study the problems of the rotary kiln of al Kufa cement plant. The heating process of the furnace starts by burning a certain amount of wood near the fuel outlet inside the rotary kiln to provide the initial combustion process of the heating oil (PDF) Cement plant operation handbook Academia.edu
احصل على السعر
Chapter 4 Cement Manufacturing and Process Control
4.4 Different Plant Design Energy is the major cost in clinker manufacturing process. The energy means the combination of thermal energy from the fuel and the electrical energy required to rotate the kiln and to run the cooler and the number of ID fans. In the cement plant, the preheater system functions as heat exchanger. The hotcement produced by about one-fifth between 1990 and 2020. Manufacturers achieved these gains mostly by improving energy efficiency in the production process, utilizing waste as a fuel, and substituting clinker with industrial waste, such as fly ash from power generation plants and blast furnace slag from steel plants. New Strengthening Sustainability in the Cement Industry
احصل على السعر
(PDF) Dry lean concrete apurba kumar Medhi Academia.edu
The work reported in this paper is based on a laboratory study carried out to investigate the feasibility of using copper slag, a by-product of copper refineries, as a partial replacement of sand in the preparation of pavement quality concrete (PQC) and dry lean concrete (DLC) mixes. A control mix for PQC was prepared with 400 kg/m 3 ofFigure 1. Overview of SeqHENS framework. The studied cement plant has an average annual clinker production of about 5600 t/d. The kiln line is a common dry process, and the raw material moisture is about 2-3%. The estimated drying demand for the raw material is about 300 kJ/kg clinker.Cement Plant an overview ScienceDirect Topics
احصل على السعر
Coal utilization in the cement and concrete industries
Coal has been the main stay of Portland cement production and remains so with coal providing around 90% of the energy consumed by cement plants around the world. It takes 200–450 kg of coal to produce 1 ton of cement. In 2015 the cement industry consumed around 4% of global coal production, around 330 Mt/year (Global Cement, 2016).
احصل على السعر>> Next:آلة مسحوق حجر الكوارتز في المملكة العربية السعودية
- feeding bottle for baby
- مستوردي آلات التعدين الجزائر
- مطحنة الألغام التعويم كسارة
- تأثير محاجر خام الحديد
- calculation of m10 grade concrete ore crusher
- مصغرة المحمول روبو مصنع الرمل
- الصين سعر الحجر المعدات
- جميع حلقات طاحون الشر
- primary vs secondary jaw crusher
- مناقصات_شركه_عثمان_عن_المينا_الحراريه_فى_اداره_المحاجر
- الفك محطم الصانع من الهند
- مصنع استخلاص العملية الجافة لخام الحديد
- transformer for the cme mobile refuse compactor
- أي أجزاء كسارة الفك
- صورة محطم لفة