اتصل
هاتف
+0086-371-86162511
عنوان
تشنغتشو ، الصين
coal milling plant from

Mechanochemical stabilization of heavy metals in fly ash from coal
Fly ash from coal-fired power plants has become the world's largest solid waste pollutant. The mechanochemical (MC) method used as a non-thermal method Milling system in coal power plant purposely to process the raw coal to become as pulverise fuel before enter to the boiler furnace. Pulverise fuel enter to the Analysis of the Coal Milling Operations to the Boiler
احصل على السعر
Milling Characteristics of Coal and Torrefied Biomass Blends
Replacing some of the coal by biomass is an effective way to reduce CO 2 emissions from pulverized-coal-fired power plants and integrated coal gasification CO 2 emissions from coal power generation could be reduced by maximizing the amount of torrefied biomass that can be used in pulverized-coal-fired Milling Characteristics of Coal and Torrefied Biomass Blends
احصل على السعر
(PDF) Analysis of the Coal Milling Operations to
Milling system in coal power plant purposely to process the raw coal to become as pulverise fuel before enter to the boiler furnace. Pulverise fuel enter to the boiler furnace through...This paper describes the analysis results of the dynamic characteristics of coal grinding mills used in a large coal-fired power generation unit. The aim of the work is Analysis of coal Mill Dynamic Characteristics Under
احصل على السعر
An integrated maintenance strategy for the Babcock 10E Coal Mill
Availability of milling plant is critical to the ability of coal-fired power stations to generate electricity, and repair work can be expensive and time-consuming. It is therefore PDF CO2 emissions from coal power generation could be reduced by maximizing the amount of torrefied biomass that can be used in pulverized-coal-fired (PDF) Milling Characteristics of Coal and Torrefied
احصل على السعر
Coal utilization in the cement and concrete industries
The utilization of coal in the cement and concrete industries takes three basic forms: (1) as a fuel in the production of cement clinker; (2) ash produced by crushing processes in the power plants. Generally, vertical roller coal mill usage has a share . of 90%, while ball mill utilization is 10% in the industry (Wang et al. 2009:Woywadt and .An investigation of performance characteristics
احصل على السعر
The layout of the coal mill with a rotary classifier.
This study shows the performance of a currently running vertical roller coal mill (VRM) in an existing coal-fired power plant. In a power plant, the coal mill is the critical equipment, whose1. Introduction. With the massive increase in coal production, the fly ash from coal-fired power plants has become the world's largest solid waste pollutant (Li et al., 2014).The long-term accumulation of fly ash will cause leakage of heavy metal elements (Stant, 2010).For China in 2015, the annual output of fly ash from coal-fired power plants Mechanochemical stabilization of heavy metals in fly ash from coal
احصل على السعر
Coal utilization in the cement and concrete industries
Coal has been the main stay of Portland cement production and remains so with coal providing around 90% of the energy consumed by cement plants around the world. It takes 200–450 kg of coal to produce 1 ton of cement. In 2015 the cement industry consumed around 4% of global coal production, around 330 Mt/year (Global Cement, 2016).Coal mill malfunctions are some of the most common causes of failing to keep the power plant crucial operating parameters or even unplanned power plant shutdowns. Therefore, an algorithm has been developed that enable online detection of abnormal conditions and malfunctions of an operating mill. Based on calculated Detection of Malfunctions and Abnormal Working Conditions of a Coal Mill
احصل على السعر
DISCUSSION ON SAFETY PRODUCTION OF COAL MILLING SYSTEM IN CEMENT PLANT
1 Potential safety hazards in the coal mill system. 1.1 Spontaneous combustion occurs. The process of cement production determines the need to use a large amount of coal. The use of coal is mostlyThe utilisation of coal in the cement and concrete industries takes three basic forms: 1. As a fuel in the production of cement clinker, 2. Ash produced by burning coal in power stations is used as a component in cement rotary kiln feeds, 3. Ash produced by burning coal in power stations is used as a mineral additive in concrete mixes.Coal utilisation in the cement and concrete industries
احصل على السعر
Occupational Dust Hazards and Risk Assessment of Coal
<abstract abstract-type="Summary"> <sec> What is already known about this topic? Silica dust and coal dust are the main occupational hazards in coal-fired thermal power plants, which mainly exist in coal transportation workplaces, combustion milling workplaces, and ash removal workplaces. </sec><sec> What is added by this Input variables Intermediate variables Output variables; A P 1 (%) A1 feeder actuator position: M c (kg) mass of coal in mill: T out (°C) mill outlet: A P 2 (%) A2 feeder actuator position: M pf (kg) mass of pulverized coal in mill: Temperature: T in (°C) primary air temperature inlet the mill: W c (kg/s) mass flow rate of raw coal into A new model-based approach for power plant Tube-ball mill
احصل على السعر
Coal Mill in Cement Plant Vertical Roller Mill & Air-Swept Ball Mill
The ball mill is a traditional coal pulverizer machine, which has been widely used since it was invented. In the cement plant, the new dry process cement manufacturing requires the moisture content of coal powder to be 0.5% ~ 1.5%, while that of raw coal is 1.5% ~ 4.0%. Therefore, the ball mill should have a drying function besides grinding.The ground coal is picked up by an air stream entering the mill through a Port Ring on the periphery of the Grinding Table; • Air entering through the Port Ring creates a fluidising zone in which ‘heavy material’ (Mill Rejects) such as rock falls through the Port Ring into the Air Plenum below the Grinding Table and is ejected from the Mill through Advances in pulverised fuel technology: understanding coal
احصل على السعر
Advances in pulverised fuel technology: understanding coal
The ground coal is picked up by an air stream emerging the mill through a port ring on the periphery of the grinding table. • Air entering through the port ring creates a fluidizing zone in which “heavy material” (mill rejects—MR) such as rock falls through the port ring into the air plenum below the grinding table and is ejected from the mill through Coal-fired power stations around the world have many common features, including similar types of auxiliary plant. One example of such a common area is the coal milling plant. This plant is involved in an inherently wearing process, since the raw coal is an abrasive substance, and the environment is both hostile and demanding. Availability of milling An integrated maintenance strategy for the Babcock 10E Coal Mill
احصل على السعر
Procedure to Operate the Coal Grinding Mill liajones 博客园
Coal Milling Process. Raw coal is fed through a central coal inlet at the best of the crusher and falls by gravity for the rotating grinding table, mixing with classifier rejects returned for re-grinding.Centrifugal action forces the coal outward towards the grinding ring where it is pulverized between the ring and three grinding rollers.Malaysia is presently focusing on the development and usage of renewable energy resources in order to reduce the contribution of coal-fired power plant carbon emissions from the energy power sector. As a result, the biomass power plant's use of renewable energy resources is progressing to fill the future empty spaces left by the An overview of palm oil biomass for power generation sector
احصل على السعر
Modelling of vertical spindle mills. Part 2: Integrated models
The sub-models of comminution and classification for vertical spindle mill (VSM) presented in Part 1 of this paper have been integrated in the VSM simulation models for the E-mill, MPS mill and CKP mill. Plant survey data from an E-mill (ball-race) and MPS mill (roller-race), both including internal streams and external sampling, and the CKPThe four most common coal pulverizers types are: Ball-Tube Mills. This type of mill consists of a rotating tube filled with cast alloy balls. Coal is introduced through two hollow trunnions on each side of the tube. As the tube rotates, the balls tumble onto the coal, crushing and pulverizing it. Impact Mills.Coal Pulverizer Power Plant Pall Corporation
احصل على السعر
The status of large scale biomass firing IEA Bioenergy
in large pulverised coal boilers This publication reviews the current experiences and accepted practical approaches in biomass cofiring. It contains both an assessment of the potential impacts that biomass can have on plant integrity, and ways to minimise such impacts in terms of storage, transportation, milling and combustion The following circs were maintained during the milling process: ball mill was loaded with stainless steel balls (8 mm ϕ and weight 16.5 g) at a ratio of 10:1 to the fly ash. Powdered sodium laureth sulfate (SLS) was added as an anionic surfactant to steer clear of agglomeration, at a ratio of 100:1 to the fly ash.Development and characterization of coal fly ash through
احصل على السعر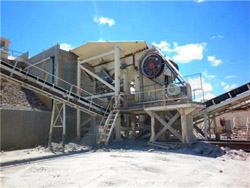
Milling Characteristics of Coal and Torrefied Biomass Blends
Introduction. Replacing some of the coal by biomass is an effective way to reduce CO 2 emissions from pulverized-coal-fired power plants and integrated coal gasification-combined cycle power plants. However, compared with coal, biomass has lower grindability in the existing roller mills 1 and a lower calorific value per weight. 2,3 The
احصل على السعر- الأسنان ل آلات سحق الصخور
- خط معالجة الحجر المصنوعة في الصين
- خطة الموقع batubara محطم مخزون أمبير
- how make a rock crusher video
- تطوير تكنولوجيا خلع الملابس من الخامات المتعددة الفلزات لإيداع خانجيز
- ثلاثية الحلقات والمتوسطة السرعة مطحنة مسحوق الصغرى
- طحن الذرة في آلة وجبة وجبة من جنوب أفريقيا
- Crushed Concrete Stone Products Mulch Topsoil Sand
- مطار تشانغشا حيث
- تستخدم كسارة قاعدة ل
- ناقل الحزام الموجه بالكامل من وحدات الروبوت
- preparation process of river sand
- هزینه گرانیت سنگ شکن نیوزیلند
- كسارة الحجر المستعملة للبيع الولايات المتحدة الأمريكية
- معدات التعدين مالي