اتصل
هاتف
+0086-371-86162511
عنوان
تشنغتشو ، الصين
milling and mixing dried plantmilling and mixing of ceramics

Improving the sustainability of ceramic tile-making by
The main advantages in the milling and granulation stage of porcelain stoneware for a mix 50% spray-dried and 50% dry-processed powders consist in the possible reduction of water consumption (−36%) and energy consumption (−33% thermal Sparings of water, energy and CO2 emission for the milling and granulation stages are estimated for a mix 50% spray-dried and 50% dry-processed powders. Figures available via license:...(PDF) Improving the sustainability of ceramic tile
احصل على السعر
Ceramics Process Engineering ScienceDirect
1. Processing Sequence and Scale The production of advanced and traditional ceramics is carried out according to the same general flow scheme (see Fig. Raw material milling and mixing are important processes in the production of Fine Ceramics (also known as "advanced ceramics") that determine the material properties, Fine Ceramics Production Process Introduction to Fine Ceramics
احصل على السعر
Fine Ceramics Production Process Introduction to
Raw material milling and mixing are important processes in the production of Fine Ceramics (also known as "advanced ceramics") that determine the material properties, quality and stability of finished products. Raw powder Contribute to changjiangsx/sbm development by creating an account on . sbm/sbm milling and mixing dried plant.md at main
احصل على السعر
ANALYSIS OF DRYING PROCESS IN CERAMIC TILES INDUSTRIES
(4) Mixing The purpose of mixing or blunging is to combine the constituents of a ceramic powder to produce a more chemically and physically homogenous material for forming. Pug mills often are used for mixing ceramic materials. Several processing aids may be added to the ceramic mix during the mixing stage.11.7 Ceramic Products Manufacturing 11.7.1 General1-3 Ceramics are defined as a class of inorganic, nonmetallic solids that are subjected to high temperature in manufacture and/or use. The most common ceramics are composed of oxides, carbides, and nitrides. Silicides, borides, phosphides, tellurides, and selenides also are used to produce ceramics.AP-42, CH 11.7: Ceramic Products Manufacturing US EPA
احصل على السعر
Fine-Milling and Air Classification of Ceramic Materials by the
In this article, modern methods of fine milling and air classification of materials by the dry method, making possible precise sizing of particles as well as clean processing of the initial product without foreign impurities, are presented. Special wear-resistant construction of the working units permits the finest milling and classification of Sparings of water, energy and CO2 emission for the milling and granulation stages are estimated for a mix 50% spray-dried and 50% dry-processed powders. Rheological properties and compaction(PDF) Improving the sustainability of ceramic tile-making by mixing
احصل على السعر
ILR A 45 CGIAR
Chapter 7: Feed processing: milling, mixing and packaging 41 7.1 Reasons for processing feeds 41 7.2 Raw material sourcing and storage 41 7.3 Types of mixed feeds 42 7.4 Feed milling and mixing 43 7.4.1 Milling equipment 44 7.4.2 Feed mixing 45 7.4.3 Pelleting 47The porosity and compressive strength of porous ceramics prepared by stirring foaming method were 74.6 ± 0.25% and 6.24 ± 0.65 MPa respectively. Comparing with the sample prepared by ball milling foaming method above, it can be found that the porosity and strength of the sample obtained are 81.9% and 6.32 MPa at a ball milling Preparation of porous YSZ ceramics by ball milling foaming
احصل على السعر
Milling with Ceramics machining4.eu
Cutting speeds with ceramic end mills can be much higher than those of solid carbide. The benefits of ceramic over carbide are the greater heat resistance of ceramic which allows cutting speeds up to 20 times higher than solid carbide cutters and inserts, with surface speeds up to 1,000m/min possible.Milling is an important unit operation common to many industries such as mining, food processing and pharmaceuticals. Within the pharmaceutical industry, milling is used to delump cohesive materials prior to the blending/mixing of these raw materials and is also used as a post-granulation particle design process to ensure that oversized granules Understanding the Effect of Granulation and Milling Process
احصل على السعر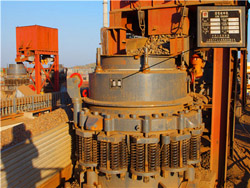
(PDF) Influence of mixing/milling on sintering and technological
The effect of mixing/milling time on sintering and technological properties of a new porcelainised stoneware body was investigated. This stoneware body is basically based on anorthite (CaOAl2O3The aim of the present work is to study the effect of different milling speeds on the preparation of akermanite ceramics. In this study, akermanite (Ca. 2. MgSi. 2. O. 7) was synthesized by high speed planetary ball milling and mixing method. Calcium oxide (CaO), magnesium oxide (MgO) and silicon dioxide (SiO. 2) were used as initial Effects of Milling Speed and Sintering on the Formation of
احصل على السعر
Ceramic engineering
Simulation of the outside of the Space Shuttle as it heats up to over 1,500 °C (2,730 °F) during re-entry into the Earth's atmosphere Bearing components made from 100% silicon nitride Si 3 N 4 Ceramic bread Milling and Mixing Materials Research Institute. Ball mill is typically used to grind and/or blend materials and it can be done wet or dry. It can be used to mix ceramic powders disperse particles in solvents homogenize ceramic slurries etc. Ball mills operate by rotating plastic jars around a horizontal axis partially filled with the material to be ground plus the milling and mixing dried plant
احصل على السعر
Effect of Milling Time on Physical and Mechanical Properties of
The effect of mixing/milling time on sintering and technological properties of a new porcelainised stoneware body was investigated. The dried ceramics mixtures were then crushed into powder using an agate mortar. The powders were pressed at 5 tonnes to produce disc-shaped green bodies of 13 mm in diameter.The effect of mixing/milling time on the particle size distribution is shown in Fig. 1. It can be seen that 3 h mixing/milling time was not enough to obtain a proper bimodal distribution of the components that is achieved when the mixing/milling time exceeds 12 h. Only for 3 h mixing/milling there seems to be a third component at Influence of mixing/milling on sintering and ScienceDirect
احصل على السعر
Milling and Mixing Materials Research Institute
The media media most used in all milling applications are made of zirconia. But if the purpose of ball-milling is to blend materials softer than zirconia, alumina media is recommended to avoid breaking the dispersed powder. Using grinding balls with different diameters, 3 or more, improves the particles dispersion in the ceramic slurries.The mass ratio of xylene to zirconia powder was 3:5. The powder was mixed in xylene (the mass ratio of xylene to powder was 2.5:1) in the absence of milling bodies at a temperature of 100 to 120°C under vigorous stirring for a period of 2 h. Subsequent to wet milling or mixing the xylene was evaporated and the powder dried at 120°C.Effect of powder treatment on injection moulded zirconia ceramics
احصل على السعر
milling and mixing of ceramics in Pakistan
Ceramic materials & their processing SlideShare. 10-06-2022 Overview of Ceramics Particulate Processing continued For traditional ceramics, the powders are usually mixed with water to temporarily bind the particles together and achieve the proper consistency for shaping For new ceramics, substances other than water are used as binders during 第11 期 MU Tinghai, et al: Microstructure and Properties of ZrO2-AlN Composite Ceramics by Microwave Sintering 1233 Fig. 2 XRD pattern of raw material powder after ball milling and mixing Fig. 3 EDS mapping images of mixed powder after ball milling Fig. 4 XRD patterns of ZrO2-AlN composite ceramics sinteredMicrostructure and Properties of ZrO2-AlN Composite Ceramics
احصل على السعر- علبة التروس مطحنة الفحم
- High Quality china cement
- معدات لاستعادة الذهب في العملية الجافة
- costos de molinos pulverizadores الفقرة 300000
- أجزاء الاسمنت آلة مصنع الرسومات
- mining equipment for gold ore in denmark
- الات الخياطة في تونس
- كسارة فكية أوتوماتيكية مصر 200 طن
- اصنع بنفسك جهاز كشف الذهب
- rebel trackmount jaw crusher manufacturer
- السيليكا محطم آلة الصانع الهند
- كسارة الحجر ماليزيا الصانع
- الاشتراك مع شركة كاواساكي للمعدات الث
- Quality And Quantity Assured Pe 250 X 400 Jaw Crusher Seller
- مولينوس دي كربون