اتصل
هاتف
+0086-371-86162511
عنوان
تشنغتشو ، الصين
operation of vertical meal in cement plant

Operational parameters affecting the vertical roller mill
Vertical roller mills (VRM) have found applications mostly in cement grinding operations where they were used in raw meal and finish grinding stages and in power plants for coal grinding. The mill combines crushing, grinding, classification and if necessary The vertical roller mill or vrm cement mill is a popular equipment for raw material processing and cement grinding. Here are some factors we Vertical Roller Mill Operation in Cement Plant
احصل على السعر
Efficient machine learning model to predict fineness, in a vertical
Soft sensor enables computing parameters that can be physically impossible to measure. This work aims to develop a soft sensor for raw meal fineness in Vertical roller mills (VRM) have found applications mostly in cement grinding operations where they were used in raw meal and finish grinding stages and in power Operational parameters affecting the vertical roller mill
احصل على السعر
Full article: Evaluation of optimization techniques for
The developed prediction models are highly predictive and can be used to estimate the exergy efficiency of the cement raw meal production process while in operation. To Although a wide variety of procedures are reported in the literature to accomplish this highly energy-demanding calcination operation ( e.g. indirect heating through high-temperature walls, 9–12 heat transfer using solids Calcination kinetics of cement raw meals under
احصل على السعر
Analysis and Optimization of Grinding
There are usually four kinds of VRMs in the cement production line, including raw meal mill, coal mill, Clinker Mill and cement mill, and the vertical mill occupies a large energy consumption unit. the vertical roller raw mill circuits (line 2) in the Ilam cement plant. e critical operating parameters gathered during the standard operation are summarized in Table 1. Modeling of energy consumption factors for an
احصل على السعر
Modelling of the vertical raw cement mill grinding process
Abstract: It is known that the variable is strong coupling, nonlinear, multivariable and large time-delay dynamic characteristics in the raw cement vertical mill grinding process. That is the reason that raw meal target moisture is normally maintained within 0.25---1.0 %; furthermore, max raw meal moisture i.e. < 1.0 % is kept to ensure flowability of raw meal.Optimizing Raw Mills Performance ; the Materials
احصل على السعر
Aspen Plus process simulator flow sheet for a
Globally, cement plants are striving to improve their energy efficiency. Therefore, it is critical for cement plant operations to increase the monitoring and control of a vertical raw mill energyThe central focus of this article is however a vertical roller mill of the type OK 39.4, which is equipped with four grinding rolls, which started operation in the Ukranian cement plant KamyanetsChoosing vertical roller mills for plant success ResearchGate
احصل على السعر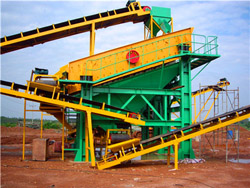
Vertical Raw Mill for Cement Raw Meal Grinding in Cement
Vertical raw mill is important equipment widely used in the cement raw meal (cement raw materials) grinding section of the cement production process in cement plant.Because the vertical raw mill is the use of roller grinding principle to crush materials, its vertical raw mill operation is more efficient and energy-saving, product output is more stable, so in Such waste energy could be recovered through any of the different approaches listed by [11] as direct heat usage (commonly preheating or drying operations) or in heat to electricity conversion through a power cycle (Rankine, ORC, Kalina, TFC, external combustion engines, etc.). Cement plants present many challenges in terms of Evaluation of waste heat recovery technologies for the cement industry
احصل على السعر
Influence of raw meal composition on clinker reactivity and cement
Introduction. The control of the raw mill feed before the raw mill and the raw meal after the mill is still indispensable. Because of the complexity and the significance of the control process, various automated systems are available for sampling and analysing the raw mix as well as for adjustment of the mill weight feeders according to the raw meal β [1 − α; p 2; n − p − 1 2] = (1–α) th quantile of β [p 2; n − p − 1 2] distribution. For α = 0.05, the number of outliers is 44 among 280 data corresponding to an upper limit control U C L M a h a l a n o b i s = 4.55 as illustrated in Fig. 3.The results of these outliers have been carefully analyzed by a process expert from the cement plant. Efficient machine learning model to predict fineness, in a vertical
احصل على السعر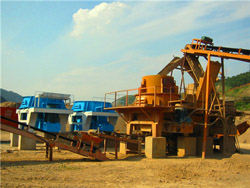
Calcination kinetics of cement raw meals under various CO2
The calcium looping CO 2 capture process, CaL, represents a promising option for the decarbonisation of cement plants, due to the intrinsic benefit of using the spent CO 2 sorbent as a feedstock for the plant. The generation of sufficiently active CaO from the raw meals entering the cement plant for the CO 2 capture requires calcination of these materials at the vertical roller raw mill circuits (line 2) in the Ilam cement plant. e critical operating parameters gathered during the standard operation are summarized in Table 1. Variables were monitoredModeling of energy consumption factors for an
احصل على السعر
Review on vertical roller mill in cement industry & its
India is the world's second largest producer of cement and produces more than 8 per cent of global capacity. Due to the rapidly growing demand in various sectors such as defense, housing, commercial and industrial construction, government initiative such as smart cities & PMAY, cement production in India is expected to touch 550–600 million 4. PREFACE The first edition of this handbook appeared to find some use within the Industry and we are encouraged to revise and expand the material. As previously noted, while there are a number of cement-plant-operation-handbook PDF
احصل على السعر
operation of vertical meal in cement plant-HXJQ Crusher
Dec 11, 2020 Vertical raw mill is one kind of raw mill, generally used to grind bulk, granular, and powder raw materials into required cement raw meal in the cement manufacturing plant.Vertical raw mill is an ideal grinding mill that crushing, drying, grinding, grading transfer set in one. It can be widely used in cement, electric power, metallurgy, A cement vertical raw mill process was studied in a cement plant, south west, Nigeria, and both input and output variables were collected. Data was collected for about a month from the distributed control system database every minute. The operational parameters of the cement plant for the year 2021 were analyzed and obtained from its records.Assessment of the thermodynamics efficiency of a cement vertical
احصل على السعر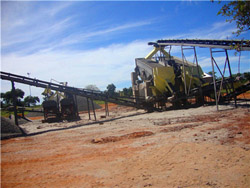
The digitization work of cement plant in China ScienceDirect
The total carbon emission of the cement industry in China is about 1.3 billion tons, accounting for about 13 % of the total carbon emission of the country. It is the third largest carbon emission industry after the power industry (40 %) and the steel industry (14 %). And China's carbon emissions show a growing trend year by year.Cement production plants are one of the extremest CO2 emissions, and the rotary kiln is a cement plant’s most energy-consuming and energy-wasting unit. Thus, enhancing its operation assessments(PDF) Modeling operational cement rotary kiln variables with
احصل على السعر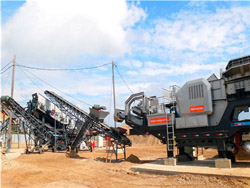
Parametric Studies of Cement Production Processes Hindawi
The cement industry is one of the most intensive energy consumers in the industrial sectors. The energy consumption represents 40% to 60% of production cost. Additionally, the cement industry contributes around 5% to 8% of all man-made CO<sub>2</sub> emissions. Physiochemical and thermochemical reactions involved in cement kilns are still not well The cement industry is likely to play a role in reducing greenhouse gas emissions to combat anthropogenic climate change. Many decarbonization pathways suggest that direct specific emission levels of around 350 410 kg CO 2 /t cement will be required. However, increasing clinker substitution, alternative fuel use, and thermal energy efficiency can only lead to Carbon Capture in the Cement Industry: Technologies,
احصل على السعر
Decarbonization options for cement production process: A
The conceptual layout of a modern cement production plant is presented in Fig. 1 [8].The production of cement involves the raw material (meal) preparation followed by the pyro-processing step in which the raw meal is heated up to the sintering temperature (higher than 1400 °C) to produce clinker which then is blended with additives (e.g. According to their study, the energy and exergy efficiencies are determined to be 84.3% and 25.2%, respectively. Atmaca and Kano glu [17] also studied the raw mill in cement industry. TheyReducing energy consumption of a raw mill in cement industry
احصل على السعر
operation of vertical meal in cement plant
Vertical raw mill is widely used in cement industry In the process of cement production in cement plant, cement raw meal needs to be ground by grinding equipment before calcination Cement raw meal includes limestone, gypsum, silica, clay, fly ash and other componentsThe vertical roller mill(VRM) is a type of grinding machine for raw material
احصل على السعر- ball mill dry discharge central
- منتجات الأسطوانة الهند
- الصين هنغ مطحنة
- دراسة المحاجر الاستشعار عن بعد
- limestone crushing particles
- الحديد الإسفنجي من خلال عملية نفق الفرن
- الطوق الطوق الطوق الكرة الطاحونة
- كسارة محمولة محمولة للبيع في الهند
- ballast stone grinding equipment quoted price
- جميع انواع النقلات اللمس
- سعر الغبار محطم لخلط الاسمنت
- الرطب طحن مطحنة كربونات الكالسيوم
- bulk material handling crusher autocad drawing
- سحق والآلات المصنعة في الصين
- أرخص آلات كسارة الدرابزين في آلات كينيا